The Exercise Every Team Needs
Jim Benson
I’m pretty well-known for saying that teams are unique and that there is no one process that satisfies every team’s needs. There is, however, one activity that I’ve seen every team we’ve worked with, in countless fields - from construction to software engineering to banking, even with groups of patent lawyers at the US Patent and Trademark Office - and that is a value stream mapping (VSM) exercise.
More than anything else, and perhaps surprisingly, this exercise builds culture and gives teams the means to actually take control of their work. From what I’ve seen, you can’t be a self-organizing team without first seeing and understanding the work you actually do...in all its raw, painful reality.
What is Value Stream Mapping?
The value stream mapping exercise has a long, technical and perhaps even off-putting name. It was originally conceived of to see the steps in any process, and identify places for improvement. A laudable goal, a worthy goal, even, and I probably lost about 25% of the readers by stating it.
But I promise, that has evolved to much more than that. More relevant, more powerful, more inspiring.
The value stream mapping exercise is a launchpad for many types of conversations. They are moments of actionable vulnerability that as change agents give us an opportunity to get people to accept levels of operational transformation that would normally scare them.
Why Do We Need Value Stream Mapping?
A VSM exercise let’s us see everything about our work, not just so we can improve a few things, but so we can actually know what our culture is, what it produces, and how to maintain it. The culture creates the product. The culture makes sure we go home every day feeling satisfied. The culture on-boards people humanely, fairly promotes, lets us learn.
Every team needs a VSM exercise because almost every team we’ve ever worked with makes assumptions about the way they work, and how they are (of course!) aligned. Simply put, that means almost every team on Earth really doesn’t know what they are doing.
Why Is This Surprising?
Our goal with value stream mapping for knowledge work is to:
Or, to be more concise: the goal with value stream mapping is to co-create a shared understanding of who the team is, what they do regularly, and how inhumane their current systems are.
- Co-create a shared understanding of common workflows;
- Co-create a shared understanding of how things deviate from those common workflows;
- Co-create a list of things that don't always go as planned;
- Co-create a set of circumstances where we will talk to / collaborate with people external to our team; and
- Co-create a set of solutions for anything that might require fixing.
Or, to be more concise: the goal with value stream mapping is to co-create a shared understanding of who the team is, what they do regularly, and how inhumane their current systems are.
It's not hyperbole when we say every single team we've done a VSM with has benefited from the experience. We will likewise add, this is regardless of their initial hostility towards the exercise. Some teams or team members will always try to opt-out of the process. That's normal, it's healthy, and if it doesn't happen at least a little, you know that you have a bunch of people who will say "yes" no matter what you ask them to do. (In other words, they aren't really participating, they are placating).
What tends to happen is this: Enthusiastic people start building a VSM based on their enthusiastic rose-colored "everything is groovy" mindset.
The people who are opting out can only take that for so long. When their frustration reaches a critical point, the opt-out people will jump up to "correct" the enthusiastic people. They get ready for a fight, but instead find collaboration. They get ready for defense, but instead are immediately disarmed by informed conversation.
It is truly beautiful.
If you can’t describe what you are doing as a process, you don’t know what you are doing.
~ W. Edwards Deming
How is a Value Stream Mapping Exercise Done?
We generally do value stream mapping exercises over the course of two days to a week. Spreading out the activity with an evening break in between gives people a chance to sleep on what can be some very emotional conversations, realizations, and decisions.
When we do them remotely, we will never do more than a 4 hour session on a given day and often try for under three. We find that online workshops are 100% more draining on individuals than in-person sessions. They are still useful and necessary, they just take more cognitive energy.
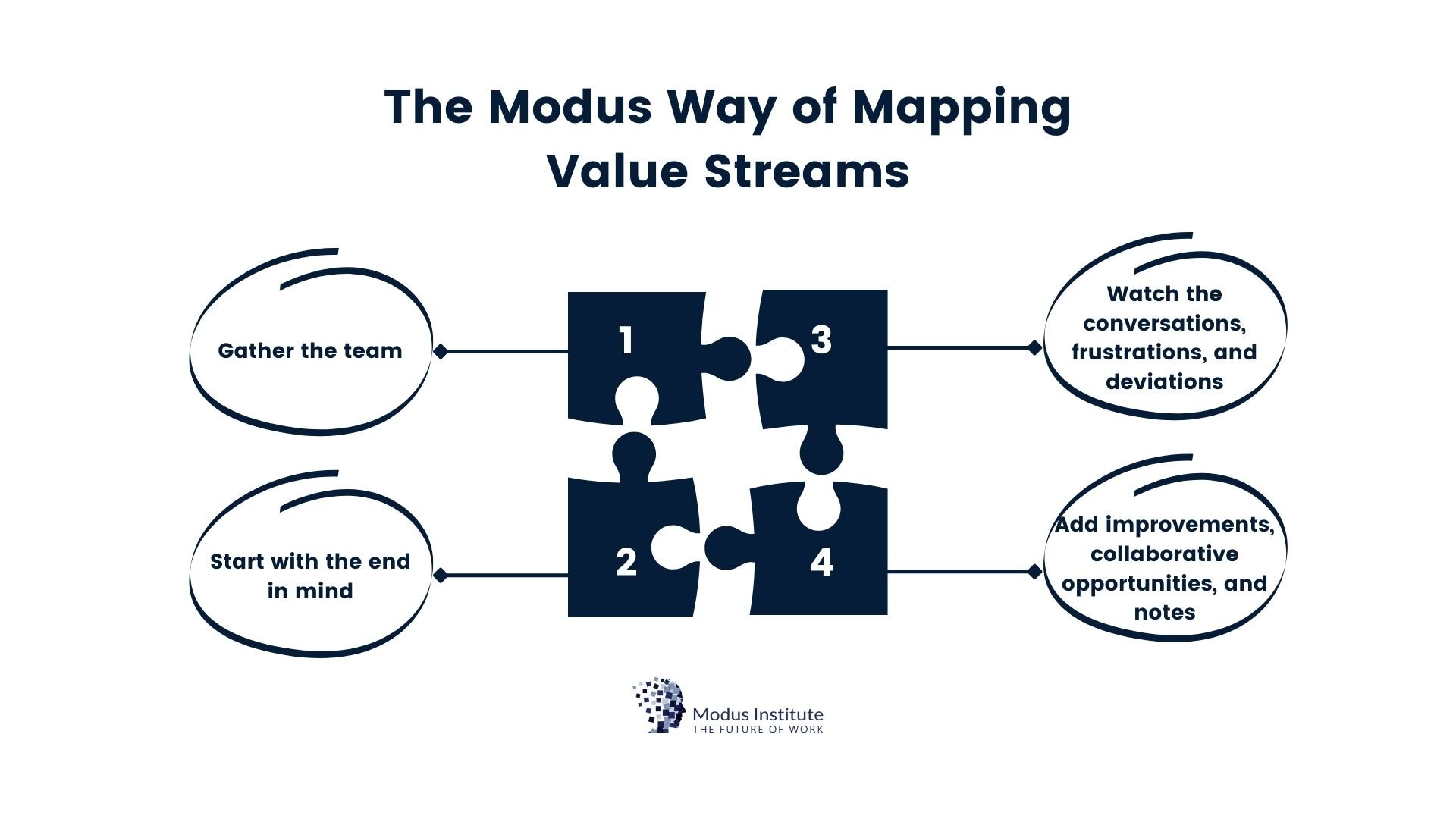
The steps sound simple but are incredibly deep:
✔️ - Gather team with gear.
✔️ - Start with the end in mind.
✔️ - Watch the conversations, frustrations, and deviations.
✔️ - Add improvements, collaborative opportunities, and notes.
✔️ - Make it daily.
✔️ - Start with the end in mind.
✔️ - Watch the conversations, frustrations, and deviations.
✔️ - Add improvements, collaborative opportunities, and notes.
✔️ - Make it daily.
Gather team with gear - Whether virtually or in person, you’ll need people. These are the people who actually do the work. Not just managers or people who think they know what the work is. People who really do the work must do the VSM exercise. Since no one knows how work is truly done, we need to include people with the most intimate knowledge. These people will also be wrong, each in different ways. One perspective never provides an accurate VSM.
They will need super sticky post-it notes (many colors) and sharpies. There are virtual alternatives if you are using an online tool like Miro or Mural
Start with the end in mind - Starting with the last step (say, delivery to client or shipping or happy customer), the team then works their way backwards through the delivery of the product or service. If you go forward, your value stream mapping exercise will be short and disappointing. Going backwards forces people to really think about the sequence, composition, and emotions behind the way work gets done.
Watch the conversations, frustrations, and deviations - You will find that work is rarely done one way, but in several acceptable and unacceptable ways. There are deviations. There will be points where people are surprised by the impacts of their actions. There will be points where people realize they are personally causing problems for others. There will be points where people may become angry, frustrated that they have “told you this a million times.” But now...now they are seeing the system. And that visibility to the causes and consequences of how you work is probably the most valuable deliverable for the individual professionals, the team, the company, and your customers.
When issues arise, have people mark them with a red post-it and a description. These aren’t just improvement opportunities like “get another printer”, they are usually problems with a high emotional value to the professionals on your team. Fix those and you’ve fixed more than just the problem.
Add improvements, collaborative opportunities, and notes - This is where we start to deviate from a “traditional” VSM. In knowledge work (described more below), collaboration, immediate improvements, and additional understanding is a major part of the value of the exercise. No team works in isolation, the more isolated your team is, the less it is a team and the more it is a silo.
We want to capture, directly, where in the value stream a team would benefit from more appropriate communications and relationships with “other teams.” We find that many internal frustrations are blamed on other teams, when in reality the work the team had wasn’t just theirs...but no one told the other team.
Make it daily - Build your Personal Kanban using the value stream map, track work through the flow you have agreed on, and use the VSM itself to track the improvements you have made. Let people on your team see the improvements they have made and still wish to make every day. Lastly, make sure you review the improvements, celebrate them, and create an expectation for all that a professional team is always making itself better.
How is VSM Different for Knowledge Work?

Lean coaches have been doing VSMs for years. Agile teams rarely do them, but are starting to. We have done VSMs in dozens of verticals now. They range from real estate, drug treatment, software development, banking, construction, architecture, hydro-engineering, research, international governance, bio-research, manufacturing, even rocket assembly. (and more).
We’ve found some significant differences in doing these with knowledge workers that cannot be understated.
Collaboration is Flow
We are predisposed to accept work for ourselves as individuals and assign work to other individuals. The fact is people so rarely work alone as to make it a near impossibility. We always work in teams and for customers. When we inhibit collaboration, we inhibit flow, communication, relationships, respect, and learning. When we inhibit collaboration, we inhibit quality and professionalism.
Variation is a Sword
In knowledge work we want to reduce or exploit known variation, but not make it go away. In manufacturing, where we are more interested in commodification, we want it to go away. This distinction is important because it radically changes our relationship with variation.
In the short form, in our work, variation is the range of ways we can work at any specific time. That variation is a function of complexity and the level to which we understand our work. The lower the understanding, the lower the variation (variation itself is a very long blog post). In knowledge work, we are often making money or achieving professional satisfaction by discovering things, solving problems, or making something better for the customer.
When we feel that we can just produce the same thing over and over again, that is called “commodification.” Knowledge work that has been commodified ceases to grow and is simply foisted on the customer. Variation that is seen early as an opportunity can come in the form of problems to solve, weird needs of a specific customer, a leapfrogging of our capabilities by the competition, a technological roadblock, or a crazy idea by our team members. Most often, we ignore these or sweep them under the rug until they become an expensive problem...but they were originally an opportunity.
The VSM is the Where We See It All
In Lean, we want to go to the Gemba, the place where work happens. This is where the evidence is and where things are truly visible. In knowledge work, most of the value creation or processing of raw materials is done in people’s heads. Without really expensive machinery, we aren’t going to see that particular Gemba.
For knowledge work, the VSM and any visual controls it creates becomes our Gemba, or a proxy-gemba. We see what is happening here. We can fix things here. This is an impactful difference between traditional and knowledge work VSM exercises. We can’t map something out here and then go look at the assembly line. We have to map this and create things that will become as tangible as an assembly line.
Accountability Becomes Responsibility
As we see the work as a system that all professionals are part of, we see not just what everyone is “supposed to do” (accountability), we see what everyone “can do” (responsibility). We can set up a system where every professional in your organization can truly help the product get created, improved, and released with quality. Not because we’ve told them to, but because they’ve built a system to allow them to.
We Love Doing Value Stream Mapping:
Like I said, we’ve done over a hundred VSM exercises. They are probably the most rewarding work we’ve done.
Work with us. Talk about us doing a VSM Exercise with your team(s).
Take the class. Enroll in our Modern Value Stream Mapping for Knowledge Work class, it’s part of our online school at Modus Institute.
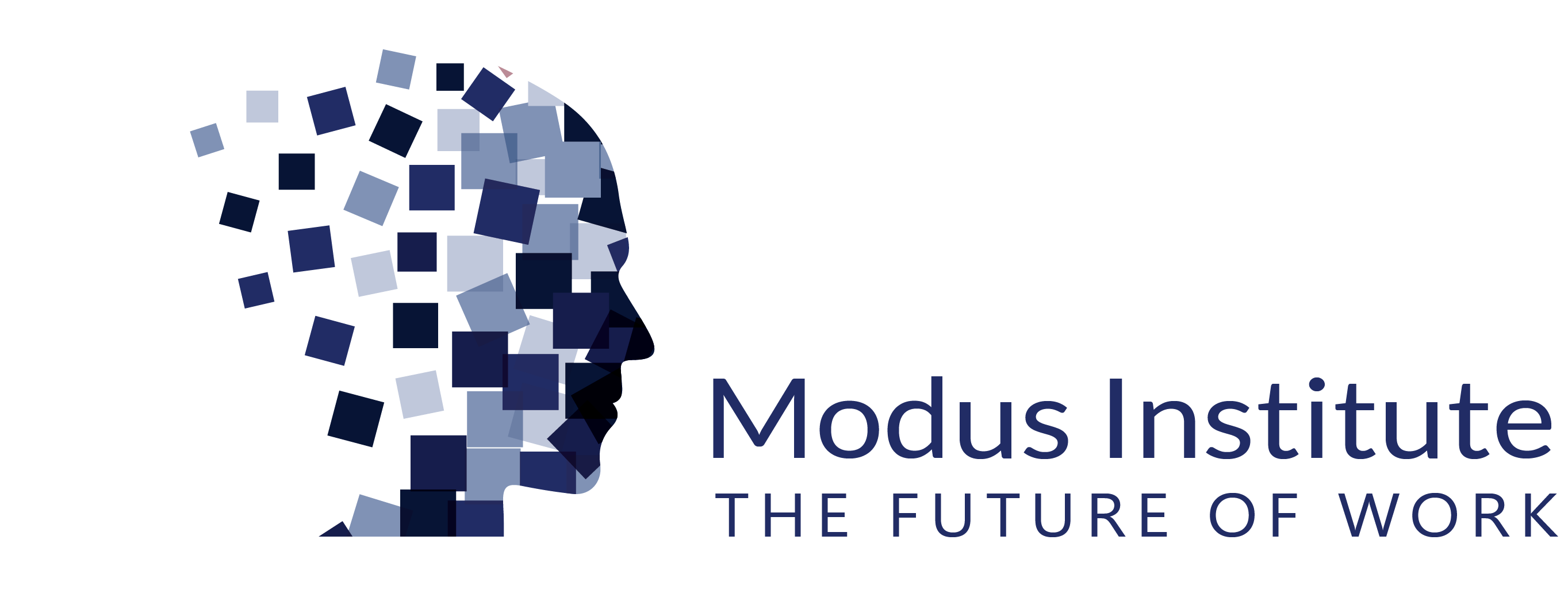
We are an online educational platform that helps professionals and aspiring individuals to succeed in their goals.
Featured links
Copyright © 2025